
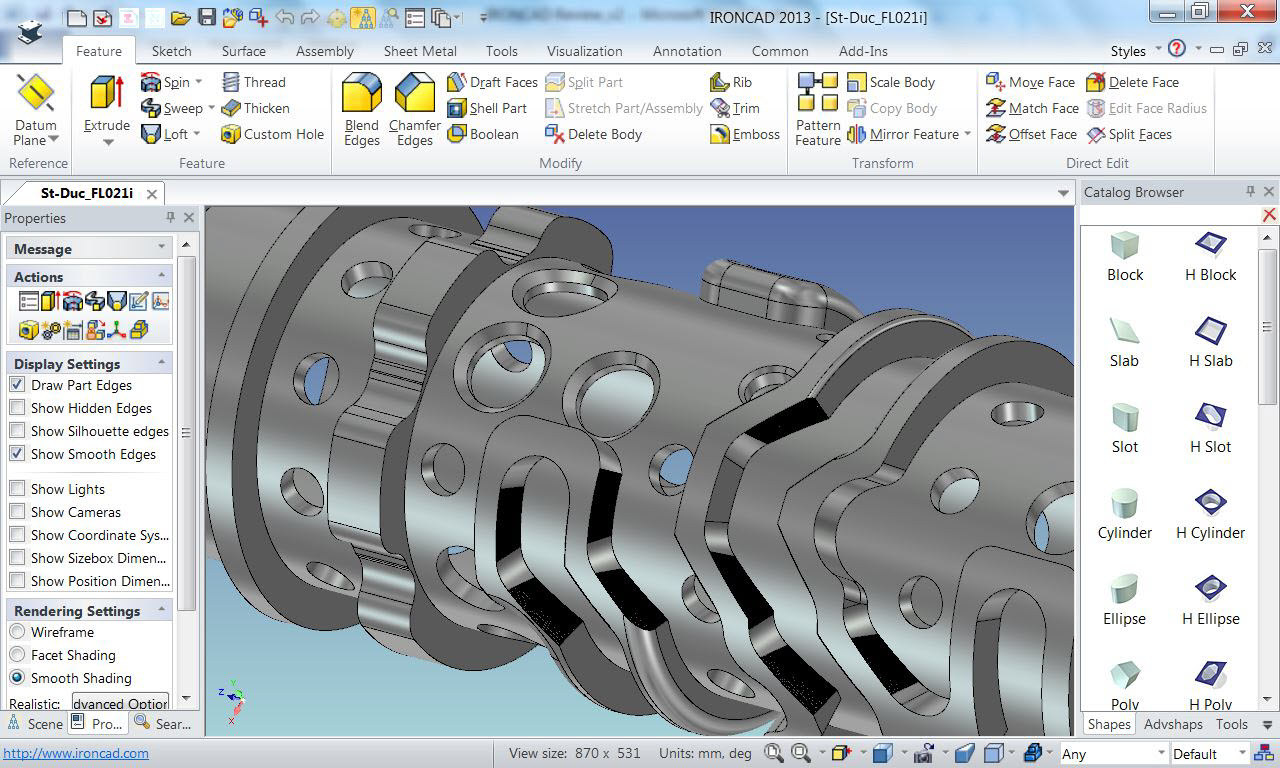
#How to use iron cad assembly update#
You’d want to be able to get the new part design file and simply update the links in your CAD assembly files vs. Say, for example, a part design changes due to shifts at a supplier. This flexibility is key for some types of product development but doesn’t necessarily work in situations where you are building multiple, complex assemblies (e.g., machines) out of standardized parts, or when parts are commonly reused among designs.
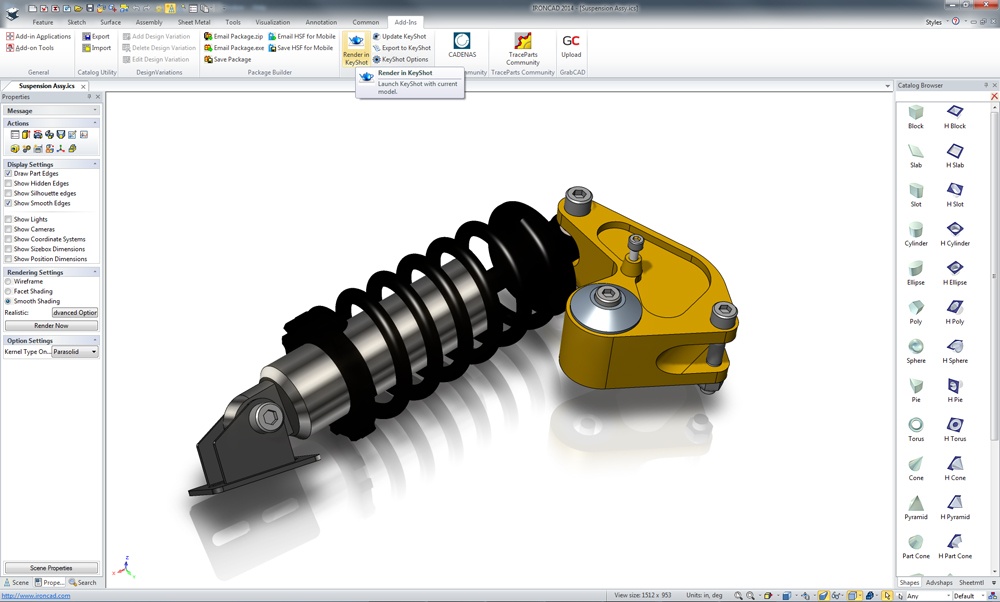
In contrast, some CAD applications are moving toward unified modeling environments where designs can be started and completed in the context of a single CAD assembly file. In situations that require frequent modifications or even positional changes - such as with bespoke machinery - it can really add up. Multiply the minutes by some factors based on how complex your model is and how often your stakeholders require changes.
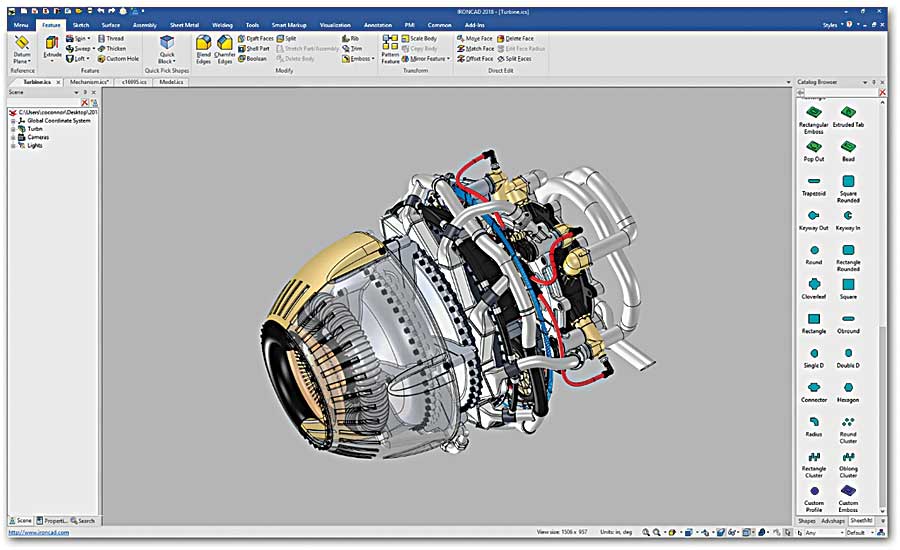
Instead, what happens is there is a lot of movement back and forth between the CAD assembly file and part files that can lead to lots of wasted time. Rarely does this process work out correctly the first time. With a part-driven approach, you won’t be able to do this in the assembly file seamlessly - you’ll have to find and alter the enclosure part file where you have limited ability to refer to other parts/sub-assemblies and hope that the updated assembly design doesn’t break during this update. As you create the assembly, you may need to change the size of the enclosure that surrounds the motor. While this makes sense from a certain perspective (e.g., during manufacturing the assembly will, in fact, be built out of parts), this setup limits a user’s ability to work on the assembly in its entirety and stunts assembly design work.įor example, say you want to be able to create an assembly that accommodates different-sized motors. The assembly itself is built in the 3D environment through a tedious mating process that joins these constituent part files. These parts live in their own files, which are then linked to by the assembly file. The Two Main Setups & Their Consequences for CAD Assembly FilesĪ traditional approach to building CAD assembly files is to start with a group of preexisting parts. The IronCAD Design Collaboration Suite’s Unified Design Environment lets you freely work back and forth between approaches, giving you the flexibility to decide how you’d like to go about creating and changing your assembly, no matter where you are in the design process. The downside of this approach is that it limits your ability to make changes that apply to all shared locations where a part or sub-assembly design is used.įortunately, there is a platform that doesn’t force you to choose between approaches when building and managing your CAD assembly file. With a single design file approach, which puts all parts of an assembly in one file and lets you alter parts directly, you can freely change parts. With traditional CAD design systems, which construct assemblies out of separate part files, it’s nearly impossible to make any fundamental changes to a CAD assembly file without also modifying constituent part files, re-linking to the assembly file, and then re-mating parts within the assembly. Many designers working on large assemblies sometimes encounter strong disconnects between how they’d ideally like to handle their CAD assembly file and how their chosen CAD platform encourages them - or even forces them - to work. Flexible CAD Assembly and Part File Management | IRONCAD, Machinery Design, Modular Design, CAD, Equipment Design, MCAD, Assembly Management
